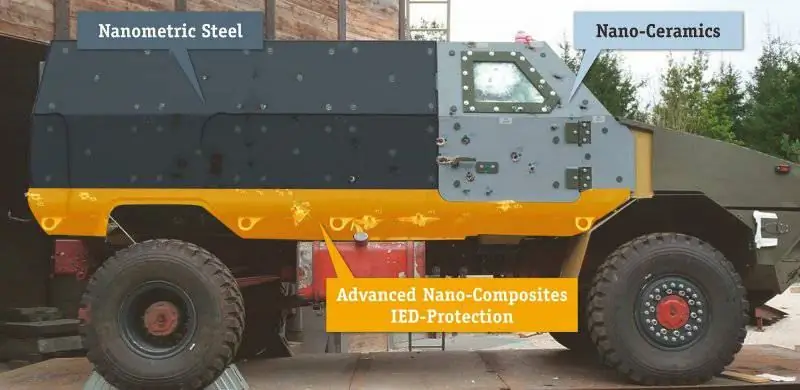
Iveco MPV använder de senaste IBD Deisenroth -skyddslösningarna, huvudsakligen baserade på nanoteknik
Passiv rustning: The Last Barrier
Pansarfordonens skrov är fortfarande tillverkade av stål, till vilka ytterligare rustningssatser är bultade. Men ju mer den grundläggande designen kan ge när det gäller ballistiskt och explosivt skydd, desto högre blir den slutliga skyddsnivån. Dessutom, även med installation av aktiva skyddssystem som förstör de attackerande projektilerna även vid inflygning, kan de resulterande högenergifragmenten orsaka allvarliga skador på fordonet, vilket igen kräver ett bra grundskydd
Det svenska företaget SSAB är en av de kända specialisterna inom rustningsmaterial, och Armox -familjen av rustningsstål är välkänd över hela världen. Familjen omfattar sex olika typer, siffran i beteckningen för stålkvaliteten indikerar den genomsnittliga Brinell -hårdheten. Även om hårdhet direkt påverkar det ballistiska skyddet, krävs seghet för att absorbera sprängningsenergi - två egenskaper som i själva verket inte kan existera tillsammans. Formbarhet förvärrar denna konflikt, eftersom höghållfasta stål i allmänhet är mindre formbara och ofta har problem med svetsbarhet.
Med tiden förbättrades de ballistiska egenskaperna hos SSAB -stål successivt: 1990 behövdes Armox 500T -stål med en tjocklek på 9 mm för att stoppa projektilen M193 / SS92 med en hastighet av 937 m / s, men tio år senare med Armox 600T -legering, bara 6 behövdes för att stoppa mm. Ytterligare tio år och 4,5 mm Armox Advance gör detsamma, även om antalet inte längre är värt det, eftersom hårdheten ligger utanför Brinell -skalan! Från en början på 70,7 kg / m2 har SSAB lyckats minska vikten till 47,1 kg / m2 på tio år och ner till 35,3 kg / m2 under det kommande decenniet. Enligt SSAB -experter förväntas ingen ytterligare signifikant minskning, den verkliga siffran för 2020 är 30 kg / m2. Företagets FoU -avdelning arbetar mer med att förbättra det befintliga materialets seghet och formbarhet än på dess hårdhet, särskilt eftersom explosionen är det största hotet i dag. Armox 440T 420-480 HB Brinell-stål har kallats föredragen energiätare och dess seghet gör det enkelt att få vilken form som helst, till exempel en solid botten. Även det hårdare Armox 500T-stål, med en hårdhet på 480-540 HB, anses vara ett material för sprängskydd.
Som nämnts ovan är det främsta kännetecknet för Armox Advanced hårdhet, därför betraktas detta stål av SSAB som en de facto keramik. Därför rekommenderar företaget starkt att inte gjuta eller svetsa det, eftersom det inte bör värmas över 100 ° C för att behålla sin hårdhet. Hur man uppnår liknande skydd och vikt i framtiden med mer formbara material är en mycket svår uppgift idag.
Bland de nya rustningsstålen ska det naturligtvis noteras Super Bainite, som introducerades hösten 2011. Det nya stålet är utvecklat av Storbritanniens DSTL Defense Science and Technology Laboratory och tillverkas på Tata Steel UK. Det uppvisar mycket bättre prestanda än standard rustning stål. Dessa egenskaper är inte bara en följd av den kemiska sammansättningen, utan också av tillverkningsprocessen, i synnerhet värmebehandling med kylning med luft och smälta salter. Slutprodukten har dubbelt så mycket ballistisk prestanda som rullad homogen rustning.
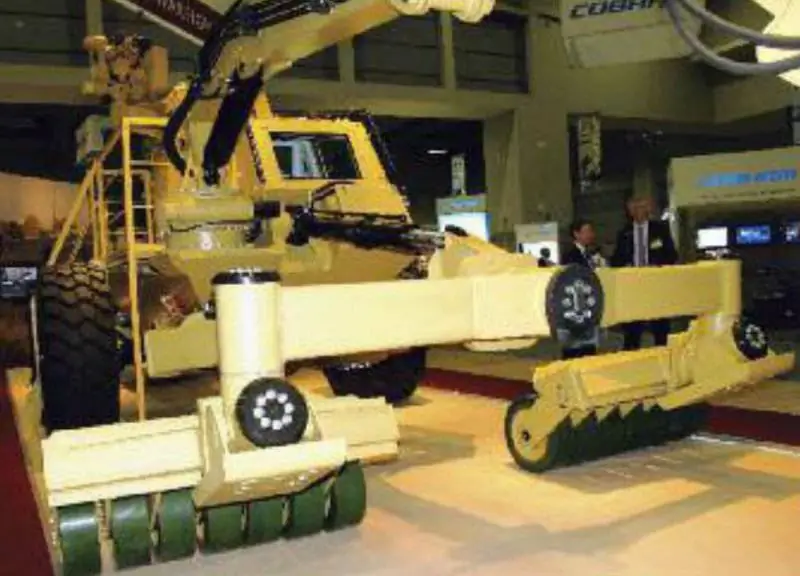
Sydafrikanska företaget Aardvark Perroc använder SSAB Armox 500 -stål i stor utsträckning i sina produkter. Detta visar att även detta stål med hög hårdhet kan absorbera stora mängder energi.
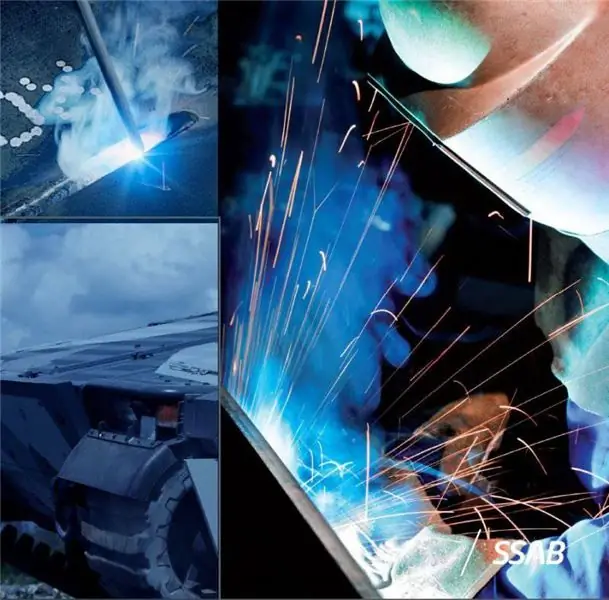
SSAB tillverkar komplexa former av sitt Armox 440T -stål, som ofta kallas en "energikätare". Den är mycket väl lämpad för strukturer som utsätts för IED. SSAB arbetar för närvarande med att göra sina rustningsstål mer formbara.
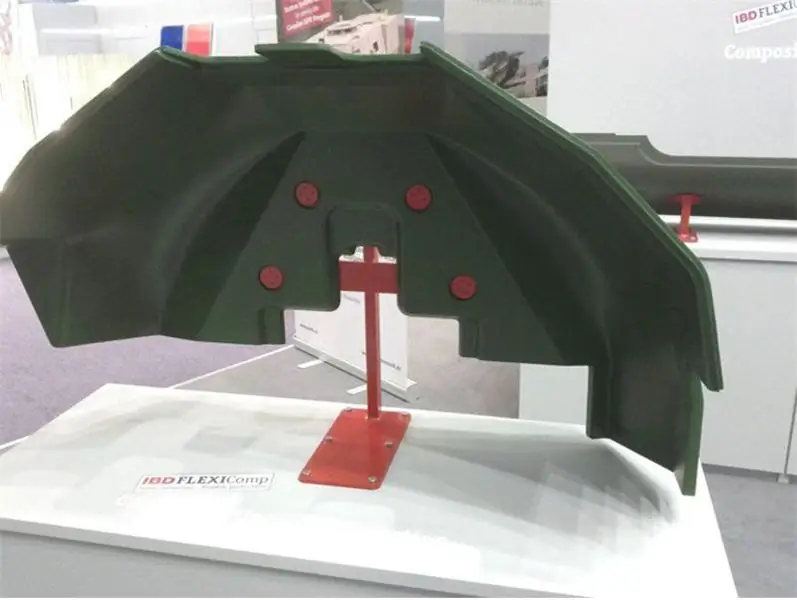
Användningen av IBD FlexiComp -foder möjliggör produktion av volymetriska säkerhetselement, vilket minskar antalet svaga punkter i det övergripande säkerhetssystemet
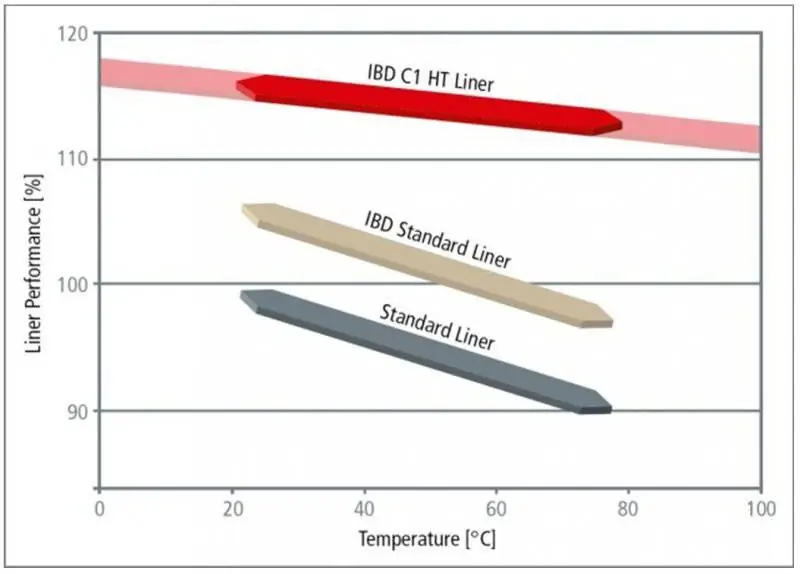
Diagram över egenskaperna hos IBD -liners som funktion av temperaturen. Effekten av höga temperaturer är ett stort problem när maskiner används i varma klimat
I december 2012 tillkännagav Lockheed Martin UK och University of Surrey en ny, enklare metod för att förbättra skyddet och överlevnaden för pansarfordon. Forskare har utvecklat en metod för behandling av keramiska material för att förbättra vidhäftningsstyrkan hos aluminiumoxidkeramik och kiselkarbidkeramik till ett kompositunderlag, vilket avsevärt ökar rustningens hållfasthet. Att fästa keramiska plattor på deras stöd har alltid varit akilleshälen för denna teknik. Resultaten visade att den nya tekniken förbättrar dragkraften. Tester har visat att när en 14,5 mm pansargenomträngande eldkula skjuts mot en rustningsplatta förblir den intakt.
Teknisk utveckling är fortfarande kärnverksamheten för IBD Deisenroth Engineering, medan passiva lösningar för närvarande läggs ut på Rheinmetall Chempro, 51% ägs av Rheinmetall Defense och 49% av familjen Deisenroth.
När Dr Ulf Deisenroth utvecklade fjärde generationens rustningsteknologi för olika typer av material var uppgiften att minska massan samtidigt som skyddsnivån bibehölls, eller vice versa, att öka skyddsnivån för en given massa, medan ny teknik lovar besparingar över 40%. De är baserade på de senaste genombrotten inom passivt skydd i samband med nanomaterial, som inkluderar nanokristallin keramik, nanometriskt stål och höghållfasta fibrer. I samarbete med ståltillverkare har IBD utvecklat höghållfasta kvävestål som nästan är i nivå med vanliga keramiska material. Dessa nya typer av stål kan appliceras på konstruktionselement, samtidigt som de kan uppnå ännu större viktbesparingar om de används i de tidiga designstadierna. När det gäller höghållfasta fibrer, till exempel IBD C1 HT Liner, har de egenskaper som är nästan 20% högre, inte bara jämfört med standardfoder, utan till och med 10% högre än andra foder från IBD; försämringen av deras parametrar med stigande temperaturer är också långsammare, vilket är särskilt viktigt med tanke på de extrema temperaturerna på moderna slagfält. Förutom nanoskala stål och nanoceramik som används på nyutvecklade maskiner har IBD också utvecklat nya kompositmateriallösningar som möjliggör produktion av element med komplexa böjda geometrier, vilket gör det möjligt att uppnå 100% täckning av det skyddade området med nästan inga ballistiska luckor. Denna lösning används särskilt vid tillverkning av bottenelement, där det minsta gapet kan äventyra hela skyddet.
IBD har också varit framgångsrika i utvecklingen av nanokompositlaminat som är så kraftigt ökade i styrka att de kan ersätta strukturella delar av en maskin samtidigt som de fungerar som ballistiskt skydd på hög nivå. På grund av deras låga ytdensitet minskar således den totala vikten av denna skyddsnivå avsevärt. Dessa kompositer är baserade på ovannämnda nanotekniska material från IBD. Specifika bindningsprocesser har utvecklats och används för att göra nanokompositlaminat av konstruktionsmaterial, så kallade IBD FlexiComp, med ökad strukturell hållfasthet och ballistisk prestanda. Med 10% mindre densitet jämfört med standardlaminat är de elastiska egenskaperna hos dessa material dubbelt så höga. Denna höga hållfasthet gör att de kan integreras i maskinens design, medan de ballistiska egenskaperna gör att den kan hantera hot på hög nivå, medan FlexiComp-material har god potential för viktminskning. Deras användning kan förkroppsligas i två olika tillvägagångssätt. Ett direkt tillvägagångssätt är att använda dem för skydd mot gruvor och IED som extra rustning i hjulhus, stänkskärmar, som gruvplattor och interna golv på avstånd. Vid gjutning av volymetriska delar kan de ersätta andra lösningar, till exempel sammansättningar monterade genom svetsning eller bultning. Det andra tillvägagångssättet är integration av sammansatta delar som luckor, motorluckor, bakdörrar och ramper. De utgör en stor andel av fordonets totala yta, och som ett resultat kommer den absoluta viktminskningen att vara mycket betydande. För STANAG 4569 Level 4 är denna viktminskning 1500 kg för en 8x8 maskin (se tabell). När det gäller tillverkningskostnader tillåter processerna som utvecklats av IBD tillverkning av sammansatta delar utan användning av autoklaver, vilket ger betydande kostnadsbesparingar, särskilt för stora komponenter, deras kostnad är jämförbar med kostnaden för komponenter som produceras med standardteknik.
Dessa komponenter tillverkas för närvarande av Rheinmetall Chempro, vars uppgift är att behärska IBD Deisenroth Engineering -tekniker, utveckla dem till en produktionsprocess för att uppnå konkurrenskraftiga priser, vidareutveckla specialiserade lösningar och följa upp dem till maskinens kvalificeringsprocess. Leveranser av komponenter gjorda med den senaste avancerade tekniken började i början av 2013, främst AMPV-maskiner från KMW-Rheinmetall och Medium Protected Vehicle från Iveco DV-KMW. Mer än ett dussin tillverkare av originalutrustning runt om i världen kommer snart att få komponenter som gör att de verkligen kan minska vikten på sina maskiner och därmed öka nyttolasten och sänka livscykelkostnaderna, säger Rheinmetalls Protection Division.
Rheinmetall Chempros passiva portfölj innehåller olika versioner av Amap -familjen (Advanced Modular Armor Protection). Denna familj använder den senaste tekniken som utvecklats av IBD. Amap -produkter kombineras vanligtvis för att ge önskat skydd mot en mängd olika hot. Bland de olika ogenomskinliga produkterna ser vi den ballistiska lösningen Amap-B, som ger skydd mot handeldvapen och medelkaliber ammunition, Amap-M gruvskydd, Amap-IED utformat för att bekämpa IED, Amap-L liners som skyddar stridsfacket genom att absorbera sekundär granat, Amap-SC mot HEAT-projektiler och slutligen Amap-X-lösningen, som skyddar mot hot som är typiska för stadsförhållanden.
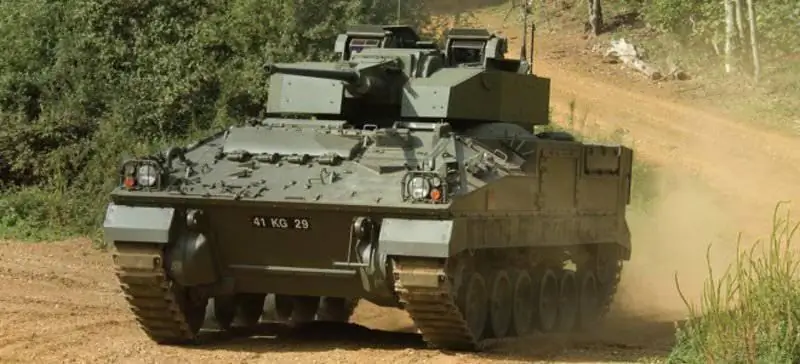
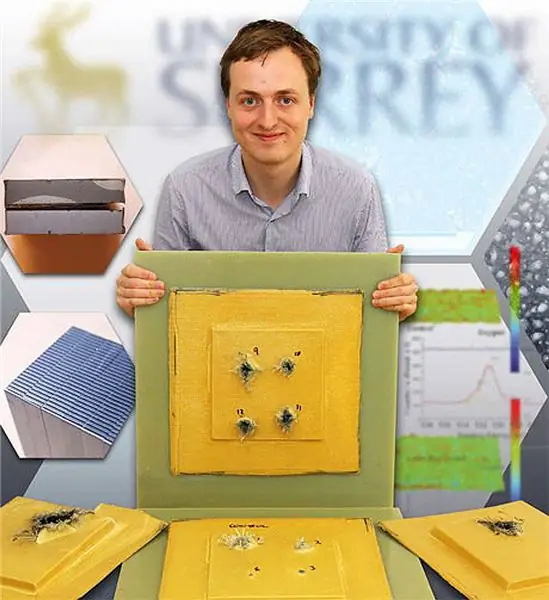
Ny bindningsteknik som utvecklats av Lockheed Martin UK och University of Surrey kan avsevärt förbättra skyddet av pansarfordon som Warrior BMP (ovan)
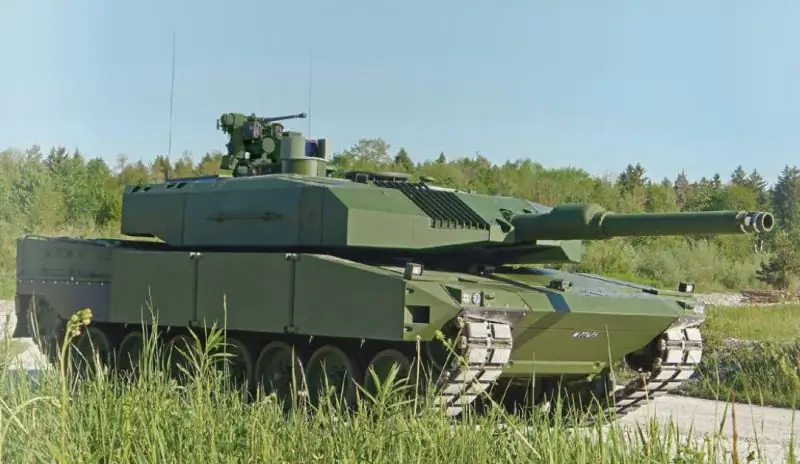
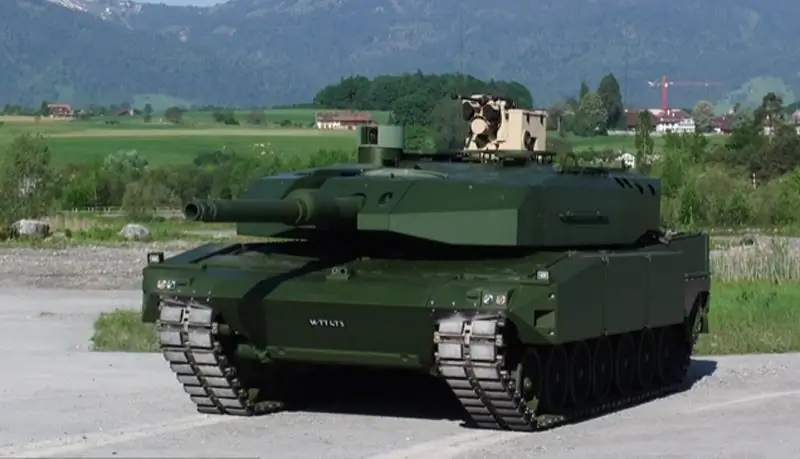
Ytterligare SidePro-ATR-moduler för MBT Leopard
Det bör noteras att inom Rheinmetall -gruppen är ett annat företag sysselsatt med passivt skydd, Rheinmetall Ballistic Protection GmbH, som fick sitt nya namn den 1 januari 2013. Tidigare kallades det Rheinmetall Verseidag Ballistic Protection GmbH. Detta företag är helägt av Rheinmetall och specialiserar sig på design och tillverkning av rustningslösningar för lätta militära fordon som använder material som keramik, avancerade metaller och specialtyger.
Även om Ruag Defense fortfarande har lösningar för dynamiskt skydd (aktiv-reaktiv rustning) i sin portfölj, ser det inte längre ut i konsumenternas ögon som ett ultramodern företag som kan öka överlevnadsförmågan hos medelstora och tunga fordon. I detta avseende vände det schweiziska företaget uppmärksamheten på att perfektionera helt passiva lösningar som klarar kinetiska och formade laddningar. SidePro-ATR-systemet går långt utöver RPG-7: s aggressivitet, eftersom det kan hantera de formade laddningarna som används i symmetriska scenarier, medan basversionen garanterar ballistiskt skydd på nivå 5. SidePro-ATR visades först för allmänheten 2012, detta system är skalbart och kan därför användas både på pansarbärare och på stridsvagnar. I sin grundversion har den en tjocklek på 400 mm, och dess massa är jämförbar med massan av en reaktiv lösning (det vill säga cirka 300 kg / m2). Detta system var kvalificerat för Leopard 2A4 -tanken. Nivån på ballistiskt skydd kan ökas avsevärt till den grad att systemet tål effekten av en 120 mm långsträckt kärna, även om inga uppgifter lämnades i detta avseende.
Skalbarheten hos SidePro-ATR gör att den kan användas i symmetriska och asymmetriska stridscenarier. En annan lösning för att bekämpa kinetisk ammunition och IED under beteckningen SidePro-KE / IED testades på det pansrade spaningsfordonet Fennek, som är i tjänst med Tyskland och Nederländerna. Den här lösningen var huvudsakligen baserad på keramik och var avsedd att bekämpa första generationens IED. Nya vägbombar, som används på olika teatrar, genererar tusentals höghastighetsfragment, och därför finns det ett behov av mycket bra multi-impact-egenskaper. Sedan dess har Ruag förfinat KE / IED-systemet genom att gå bort från keramik och använda icke-expanderbara påsar med flera lager. Den nya SidePro-KE / IED-lösningen, tillgänglig sedan 2012, erbjuder nivå 4 / nivå 5 skydd mot kinetiska vapen och har extremt hög prestanda med flera slag. Förutsatt att chassit är tillverkat av 7 mm ballistiskt stål, kan en 30 mm panel ge det fullständiga skyddet som krävs, med KE / IED -systemet som möjliggör minsta viktökning, endast beroende på fordonstyp. Denna lösning väntar på flera tillverkare.
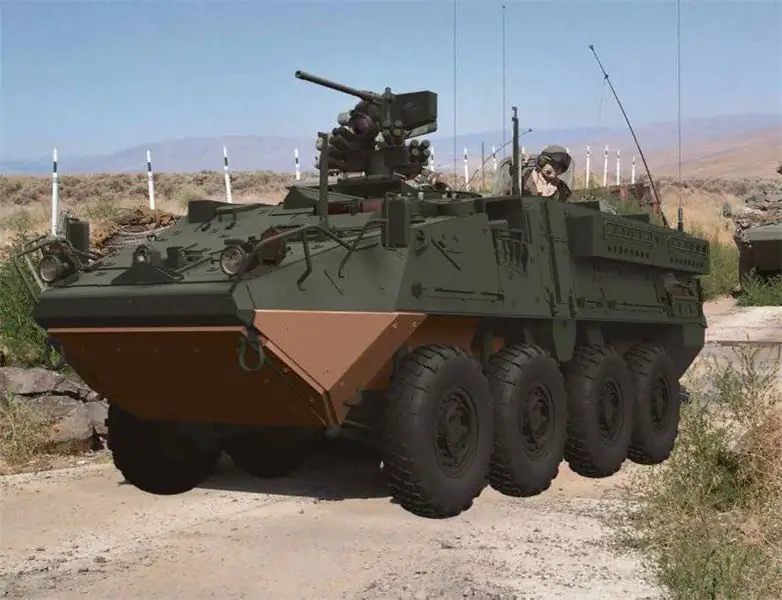
Ruag har slutfört SidePro KE / IED. Fotomontage visar elementen i ett system utformat för att motverka nya enheter som genererar flera fragment.
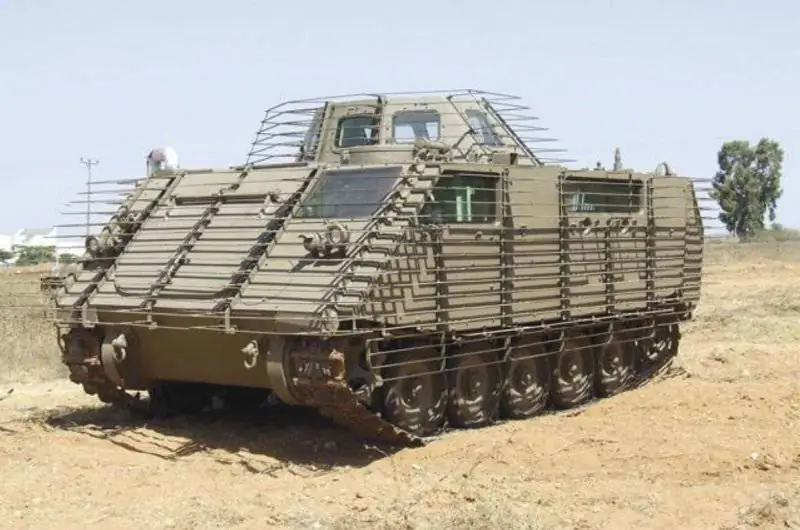
BTR M113, utrustad med ett passivt anti-RPG-system Iron Wall från Israel Military Industries, som kombinerar passiv och gitter rustning
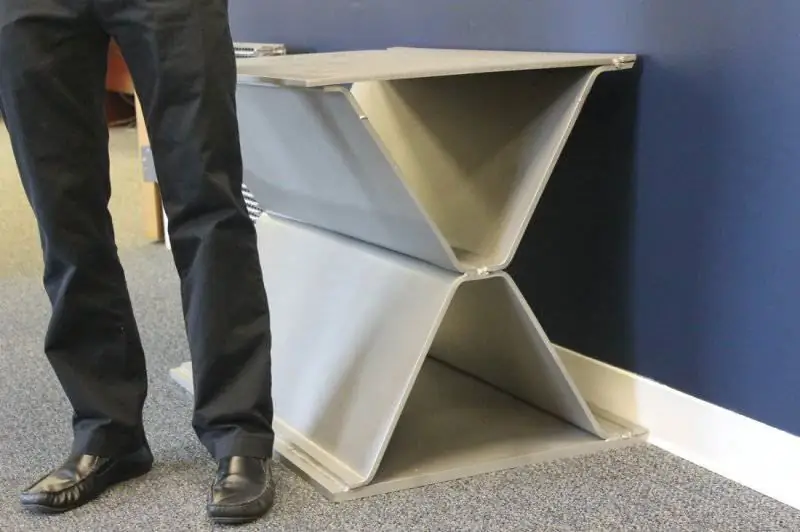
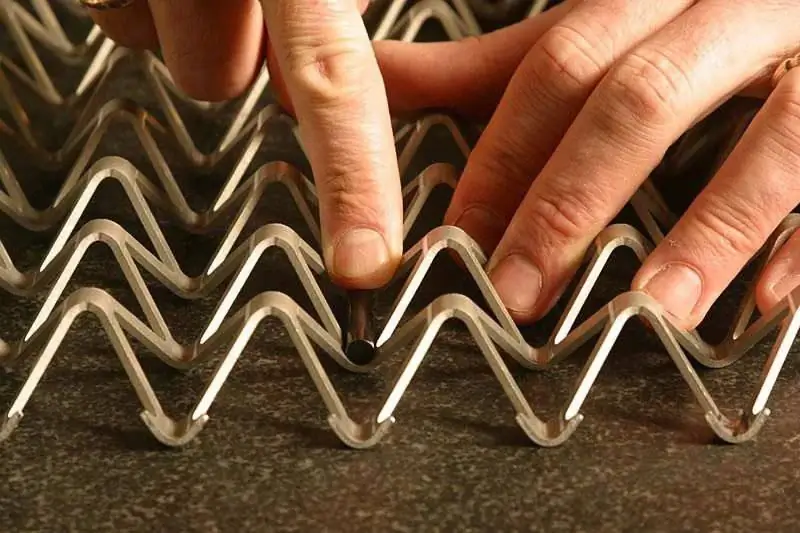
Ceradyne och Cellular Materials International har utvecklat en bottensköld baserad på CMI MicroTruss aluminiumhonungskaka som absorberar upp till en tredjedel av energin som genereras av en explosion. Nedan finns en närbild av MicroTruss-materialet.
Viktminskningsexempel för en 8 x 8 -maskin med komponenter tillverkade av IBD FLEXICOMP
Vikt i kg
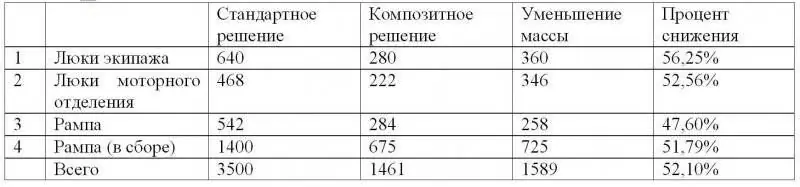
Plasan Sasa är fortfarande en av nyckelspelarna i den passiva bokningsbranschen. Inga tekniska detaljer ges på detta område, medan företaget är aktivt både i ytterligare bokningar och i prefabricerade byggnader. Det andra tillvägagångssättet togs med utvecklingen av Mrap från Navistar MaxxPro och M-ATV från Oshkosh. "Detta gör att vi kan öka produktionen med hjälp av en personalstyrka utan svetsfärdigheter, eftersom vår Lego-stil är baserad på block som innehåller alla komponenter som kan monteras på ett minimum av tid", säger en företagskälla. Några av de mer än tvåhundra ingenjörerna i företaget arbetar med nya lösningar som kan bero på uppkomsten av nya material eller innovativa geometriska lösningar. Systemmetoden förblir kärnan i skyddscykeln.
IMI har nyligen utvecklat en rad passiva och reaktiva lösningar för att motverka de senaste typerna av IED, inklusive de olika typerna av EFP eller SFF (Self Formed Fragmentation) "shock cores" och de senaste RPG -modellerna. Företaget har föreslagit en passiv Iron Wall -lösning baserad på en kombination av metall och kompositer kompletterade med gitterpansar. Beroende på vilken skyddsnivå som krävs kan tjockleken variera mellan 110 och 150 mm och vikten mellan 200 och 230 kg / m2. Iron Wall genomgår för närvarande militära prövningar med den israeliska armén.
IMI erbjuder också sin gitter rustning som ett fristående system. L -VAS (Light Vehicle Armour System - pansarsystem för lätta fordon) är utformat för att skydda fordon som pansarbärare. För att minska vikten är systemet baserat på kompositmaterial och reaktiva element, de senare innehåller ett minimum av energimaterial. Detta minskar indirekta förluster, och typen av material undviker risken för sekundär detonation av intilliggande element. Enligt IMI skyddar L-VAS-systemet också mot 14,5 mm rustningsgenombrytande rundor och artillerifragment. Systemet är fullt kvalificerat i Israel för sin M113 APC och har en specifik vikt på cirka 200 kg / m2.
Ett tyngre vågsystem erbjuds också. Denna reaktiva rustning, bestående av metall och sammansatta element, är utformad för att bekämpa tre huvudhot: RPG, SFF och EFP. IMI har utfört omfattande tester och fortsätter för närvarande med kvalifikationer för att börja producera en lösning med en tjocklek på 350 - 400 mm och en vikt på 430 - 450 kg / m2 i slutet av 2013.
Ceradyne är en annan stor aktör inom passiv bokning. Enligt Mark King, president för Ceradyne, är stål fortfarande det viktigaste materialet i bokningsverksamheten, med målet att förbättra prestanda och minska kostnaderna. "I USA är drivkraften främst kostnaden för att förvärva ett fordon, inte kostnaden för dess livslängd, och det motverkar uppgraderingar", sa King vid AUSA -konferensen 2012. i USA låg tonvikten på kvantitet, vilket tog europeiska utvecklare av skyddssystem före amerikanska. King betonade emellertid att Amerika för närvarande går framåt, främst med fokus på explosionsskyddsmedel, eftersom ballistiskt skydd ses som ett löst problem. Intresset för den amerikanska armén, återigen visat att lösa problemet med att skydda botten på sådana fordon som till exempel Humvee (endast 20 miljoner dollar för utveckling), bedöms positivt av King. Ceradyne är en av dem som definitivt kommer att tävla om ett kontrakt för sin modernisering. Kravet ger maximalt skydd med betydande viktbesparingar för att minska påverkan på maskinens prestanda.
Ceradyne har utvecklat en MicroTruss -lösning från Cellular Materials International Inc (CMI). Detta porösa aluminiumlegeringsmaterial har en densitet på 58 kg / m2 jämfört med densiteten på 112 kg / m2 för en ekvivalent monolitisk metalllösning. Denna lösning skiljer sig i kroppens "V" -vinkel lika med bara 5 °, vilket är tillräckligt för att reflektera blåsvågen och har en massa på 300 kg. MicroTruss garanterar absorption av upp till 30% av explosionsenergin, vilket inte bara begränsar påverkan på besättningskapseln utan också minskar fordonets vertikala rörelse. Ceradyne är också starkt involverad i bokningsprogrammet Flyer Gen.2, som är inriktat på Special Operations Forces -projektet för GMV 1.1. För att upprätthålla transportbarhet inuti V-22, CH-47D och CH-53E helikoptrar när massa och bredd måste hållas inom vissa gränser, har företaget utvecklat ett kit som ger en B6 (.357 Magnum) nivå av ballistiskt skydd för dörrarna och tak.
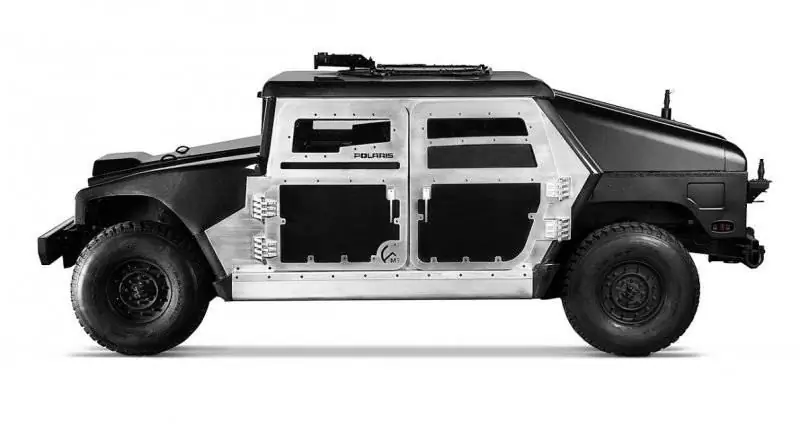
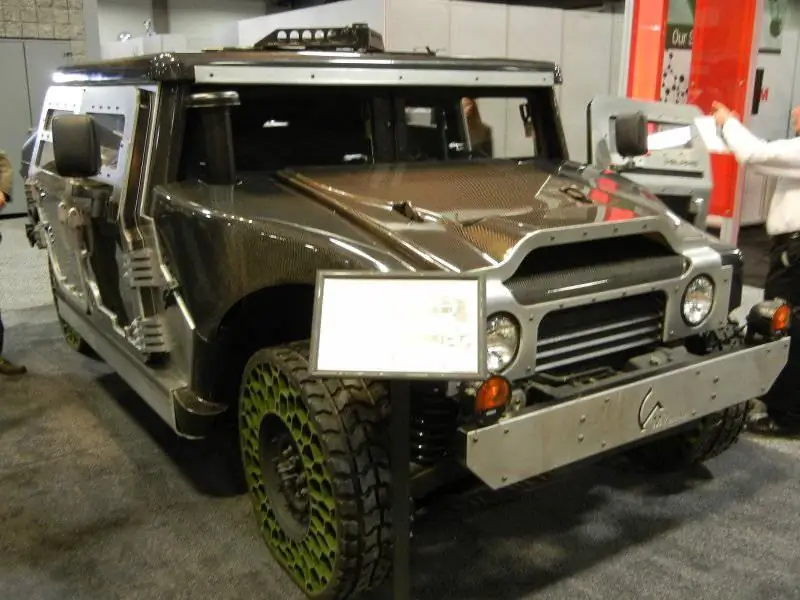
Polaris Defense och M9 Defense Armor Technology har utvecklat en hybrid stålkomposit strukturell rustning som avsevärt kan minska Humvees egen vikt samtidigt som skyddsnivåerna bibehålls. Prototypen på bilden till höger har en egenvikt på endast 3400 kg, vilket är nästan 50% mindre än Humvee med nivå 3 -skydd.(Observera bilens hjul längst ner)
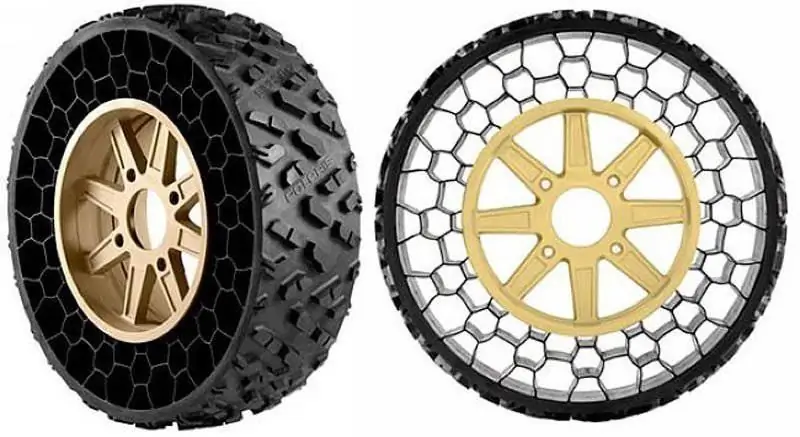
Skydd handlar också om att inte lämnas kvar på slagfältet vid ett punkterat hjul. Icke-pneumatiska hjul från Polaris Defense garanterar betydligt bättre hållbarhet jämfört med vanliga däck och tål en 12,7 mm kula. För närvarande är de tillgängliga inte bara för bilar, inklusive Hummer -klassen, men nu utvecklas dessa hjul också för de tyngre Mraps -bilarna.
Ceradyne deltar också i programmet Marines Personnel Carrier i samarbete med Lockheed Martin och Patria på ett Marine Corps -fordon baserat på finska Patria AMV. Det är värt att notera att den 28 november 2012 tillkännagavs att Ceradyne förvärvades av 3M -gruppen, vilket gör att den kan investera mer i FoU och innovativa lösningar.
Integration av design och skydd är en mycket eftertraktad lösning för lätta fordon. Vid AUSA 2012 visade Polaris Defense en prototyp av Humvee -fordon med ett nytt koncept som det utvecklade i samarbete med M9 Defense. Utmaningen är att minska vikten samtidigt som man bibehåller och ökar skyddsnivåerna. För att göra detta tog Polaris-M9-teamet bort alla överliggande rustningar för att ta en titt på strukturella rustningskonceptet. Sedan togs allt bort från bilen, bara ett chassi var kvar och sedan sattes en lätt hybrid (stålkompositmaterial) på den. Denna strukturella rustning kan ge nivå 3-skydd med en massa på 70 kg / m2 och med en massa på 83 kg / m2, den klarar en 12,7 x 99 mm kula, även om Polaris-M9-gruppen är säker på att de kan nå nivå 3+ (12, 7 mm rustningspenningskula). Polaris-M9-lösningen skyddar också motorn. Medan det vanliga pansarfordonet Hummer väger cirka 6 350 kg tillåter den föreslagna lösningen dess vikt att minska till 3400 kg. Hybridstrukturen har ett icke-exotiskt material, vilket gör att Polaris-M9-teamet kan prata om kostnaden för den nya lösningen, jämförbar med kostnaden för de nuvarande lösningarna. Dessutom formas detta material till komplexa former, vilket bland annat resulterar i sömlösa V-formade bottnar. Uppnå önskad form uppnås genom hydraulisk formning - en höghastighetsprocess som hjälper till att minska kostnaderna. Enligt Polaris-M9-teamet kan denna teknik minska vikten med 40 procent.
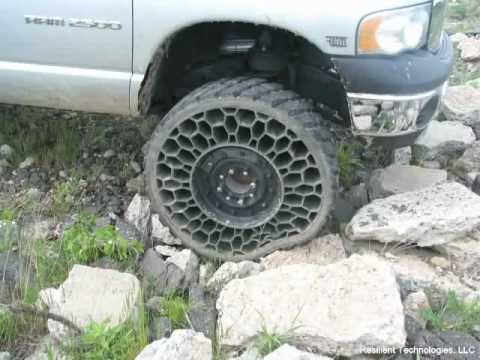
Demonstration av icke-pneumatiska hjul från Polaris Defense
Försvarsekvationen innehåller en annan term som direkt relaterar till rörlighet - hjulet. Efter förvärvet av Resilient Technologies erbjuder Polaris Defense nu Non-Pneumatic Wheels (NPT). Hjulförbrukning är ett av de viktigaste logistiska problemen i en turbinmotor och NPT -lösningen kommer i många fall att hjälpa till att lösa det. Enligt kommandot från specialoperationsstyrkorna i Afghanistan färdas konventionella däck cirka 1300 km, medan ett NPT -hjul punkterat av en 12,7 mm kula kan färdas mer än 8000 km och därför förskjuta reservhjul från leveranskedjan, samtidigt som körkvaliteten förbättras. NPT -prototyper har redan gjorts för Hummer -fordon. Det nuvarande målet är en uppsättning NPT -hjul för 7,7 ton maskinen, vilket är nästan totalvikten för JLTV -varianten för allmänna ändamål. Enligt företagsrepresentanter visade modellering att massan kan nå 18 ton, med andra ord, hjulen tål en Mrap -klassbil. När nyttolasten ökar förblir tekniken densamma, och företagets simuleringsprogram tillåter mycket exakta förutsägelser. Det som kommer att förändras är materialet som måste anpassa sig till massan, som i sin tur ännu inte har dykt upp i framtiden.