Krig är känt för att vara den bästa framstegsmotorn. Tankindustrin i Sovjetunionen gjorde ett svindlande kvalitativt språng på bara några få krigsår. Den sanna kronan av detta var tankarna i IS -serien.
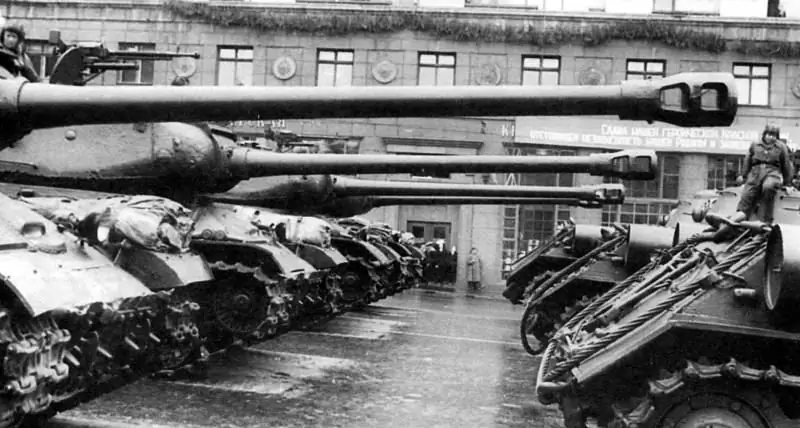
Magnitogorsk recept
I den tidigare delen av berättelsen handlade det om den 70L gjutna rustning med hög hårdhet som användes för tornen på IS-tankarna. Pansarutvecklarna från TsNII-48 var långt ifrån den första erfarenheten av att skapa skydd för tunga stridsvagnar.
Innan Kursk Bulge, som blev en katalysator för utvecklingen av inhemsk tungtankbyggnad, var huvudsyftet med moderniseringen KV -tanken. Inledningsvis var allt arbete inriktat på att minska andelen knappa legeringstillsatser i rustningens sammansättning. Till och med namnet i TsNII -48 kom med ett lämpligt namn - ekonomiskt legerat stål. Den ursprungliga rustningen av märket FD-7954, med vilken KV-tanken gick in i det stora patriotiska kriget, innehöll enligt tekniska krav upp till 0,45% molybden, 2,7% nickel och krom.
I slutet av 1941 skapade en grupp forskare under ledning av Andrei Sergejevitsj Zavyalov vid Pansarinstitutet ett recept på stål FD -6633 eller 49C, där molybden inte krävde mer än 0,3%, krom - upp till 2,3%och nickel - upp till 1, 5%. Med tanke på att tankarna i KV -serien från andra hälften av 1941 till 1943 samlades omkring 4 tusen exemplar kan man föreställa sig mängden verkliga besparingar i legeringsmetaller.
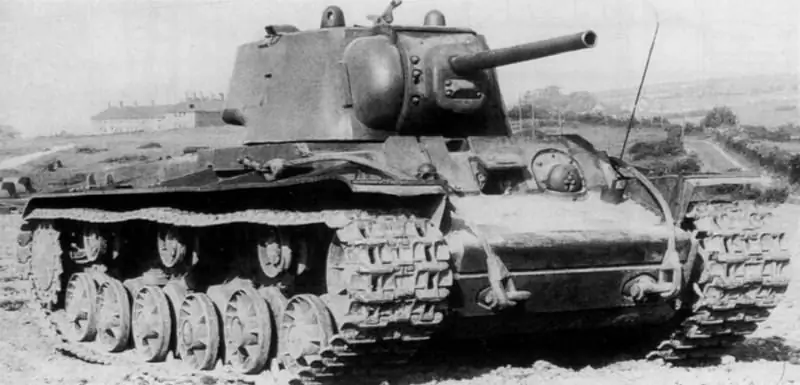
Hemligheten till framgång
Hemligheten bakom metallurgernas framgångar ligger i studien av parametrarna för bildandet av fibrös frakturfraktur - huvudparametern för projektilresistens. Det visade sig att du kan klara dig utan en betydande andel legeringselement genom att helt enkelt ändra rustningens kylhastighet under släckning. Men det här är enkelt i ord - hur många preliminära experiment och smältningar metallurgister fick göra, är det bara de nu klassificerade arkiven som kommer att kunna berätta.
På Magnitogorsk Metallurgical Plant 1941 erhölls de första prototyperna av 49C-stål, som inte var sämre än den traditionella rustningen "före kriget". I synnerhet visade beskjutningen av 76 mm-kanonen full överensstämmelse med de taktiska kraven för tanken. Och sedan 1942 har endast rustning med namnet 49C använts för KV -serien. Det är värt att komma ihåg att förbrukningen av krom, molybden och nickel har minskat avsevärt.
Sökandet efter nya rustningsformuleringar för tung utrustning slutade inte där. 1942 "svetsades" stål GD-63-3, helt utan brist på krom och nickel. Till viss del ersattes nickel med mangan - dess andel ökade mer än tre gånger (upp till 1,43%). Prototyper av den nya rustningen sköts på. Och de visade sig vara ganska lämpliga för massanvändning i utformningen av KV. Men Klim Voroshilov -stridsvagnarna med rustning av medelhårdhet gick i pension. Och platsen för tunga fordon togs av "Joseph Stalin" -fordon med rustning med hög hårdhet.
Valsad rustning 51C
Om 70L-rustningen för IS-2-torn kan kastas, fungerade detta trick inte med tankens skrovdelar. Här stod ingenjörer inför två problem på en gång - skapandet av rustning med hög hårdhet med stor tjocklek och behovet av att svetsa in den i ett färdigt skrov.
Alla som är intresserade är förmodligen redan medvetna om problemen som orsakas av svetsningen av T -34 -rustningen - det finns en stor sannolikhet för sprickbildning i svetsområdet. IS-2 var inget undantag. Och dess kropp var ursprungligen tänkt att tillagas från slutligen värmebehandlade delar.
Inse vilka svårigheter och faror en sådan teknisk lösning skulle medföra i militär operation, ändrade TsNII-48-specialister tankproduktionscykeln. Som ett resultat, 1943, vid Ural Heavy Machine Building Plant och Chelyabinsk-anläggningen nr 200, beslutades att IS-2-skrovet skulle tillagas av pansarplattor som bara hade passerat en hög semester efter rullning. Det är i själva verket skrovet på en tung tank monterat av "rått" stål. Detta minskade kraftigt svetsdefekterna på den 51C rullade rustningen med hög hårdhet.
Den slutliga värmebehandlingen genom uppvärmning före släckning utfördes redan på tankens svetsade kropp, efter att först ha förstärkt den med inre stag. Kroppen förvarades i ugnen i tre timmar. Och sedan, på specialanordningar, överfördes de till en vattendämpningstank och förvarades i den i 15 minuter. Dessutom steg vattentemperaturen i kyltanken från 30 till 55 ° C. Yttemperaturen på kroppen efter att ha tagits bort från vattnet var 100-150 ° С. Och det är inte allt.
Efter släckning utsattes kroppen omedelbart för lågt temperering i en cirkulerande ugn vid en temperatur av 280-320 ° С med hållning efter att ha nått denna temperatur i 10-12 timmar. Den låga tempereringen av gjutna torn från 70L rustning utfördes på ett liknande sätt. Intressant nog var sprickkontrollen i de experimentella IS-2-skroven i fyra månader, när de första produktionstankarna lämnade fabriksportarna.
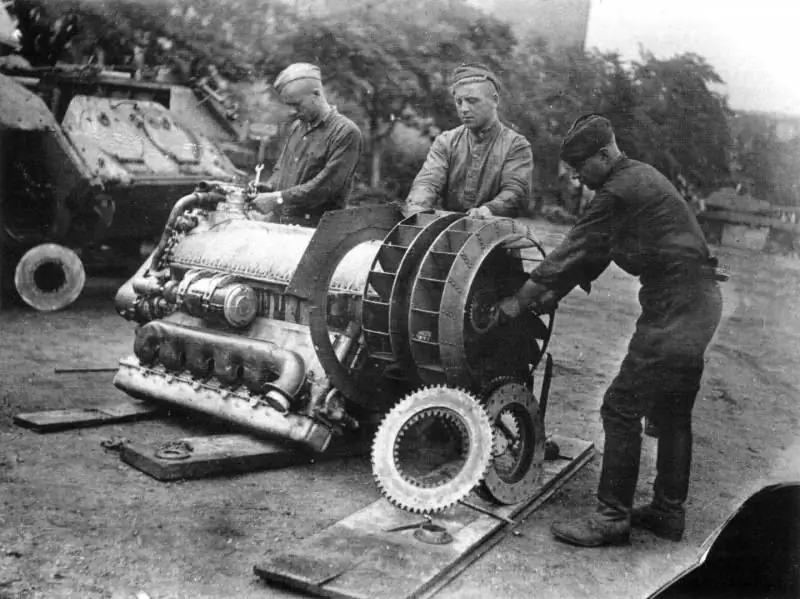
Kemisk sammansättning
Vad var den 51C rullade rustningen som blev den viktigaste för IS-2, ISU-122 och ISU-152? Det är ett djuphärdande stål för stora rustningstjocklekar med följande kemiska sammansättning (%):
C 0, 18-0, 24
Mn 0, 70-1, 0
Si 1, 20-1, 60
Cr 1, 0-1, 5
Ni 3,0-3,8
Mån 0, 20-0, 40
P ≤ 0,035
S ≤ 0,035.
I jämförelse med gjutna pansar 70L hade 51C -valsat stål en högre andel molybden och nickel, vilket garanterade en ökning av härdbarheten upp till 200 mm. När skrov på tunga tankar avfyrades med 88 mm skal visade det sig att rustningen med hög hårdhet var mycket överlägsen i hållbarhet än sina föregångare med medelhårdhet. Frågan om att placera rullad rustning 51C löstes omedelbart.
Smart svetsning
Ett viktigt bidrag till framgången för utvecklingen av rustningsproduktion av tankar i IS -serien gjordes genom automatisk svetsning av stål under ett flusslager. Eftersom det var omöjligt att överföra hela processen att tillverka ett tankpansarskrov till sådan svetsning i början av 1944, fokuserade ingenjörerna på att automatisera de mest förlängda och mekaniskt laddade sömmarna.
Vid fabriken i Chelyabinsk nr 200, vid montering av skrovet på den tunga tanken IS-2, kunde endast 25% av alla svetsar automatiseras. I mitten av 1944 kunde Tankograd automatisera 18% av alla möjliga 25% av svetsarna. Den totala längden på de svetsade sömmarna längs skrovet på IS-2 tunga tanken var 410 löpmeter, varav 80 löpmeter utfördes med den automatiska svetsmetoden.
Detta resultat har lett till betydande besparingar i knappa resurser och el. Det var möjligt att frigöra upp till 50 kvalificerade manuella svetsare (deras arbetskostnader i mängden 15 400 arbetstimmar) och spara 48 000 kilowattimmar el. Minskad förbrukning av elektroder (cirka 20 000 kg, austenitisk - 6 000 kg), syre (med 1 440 kubikmeter).
Tiden för svetsning har också minskat avsevärt. Till exempel, svetsning av botten och tornbox till sidorna med en sexton meters söm tog 9,5 manstimmar i manuellt läge, och endast 2. En söm med liknande längd som förbinder botten med sidorna av tankskrovet i automatiskt läge krävs 3 arbetstimmar (i manual direkt 11, 4). Samtidigt kan högkvalificerade svetsare ersättas av okvalificerade arbetare inom automatisk svetsning.
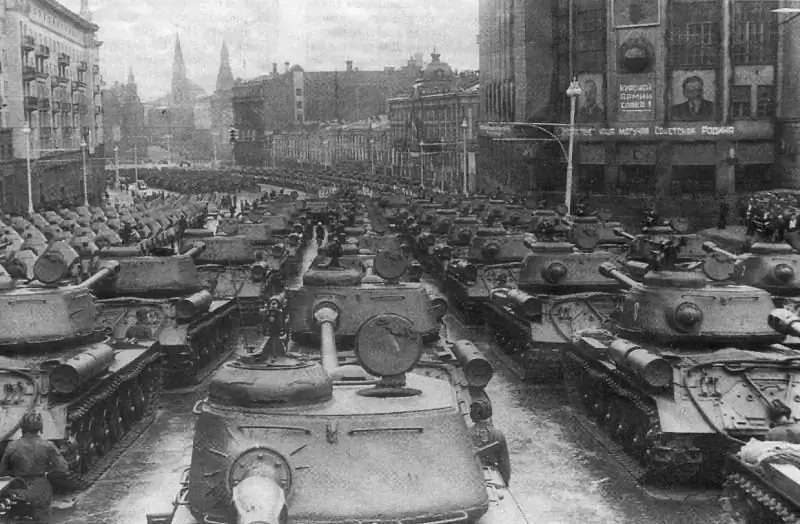
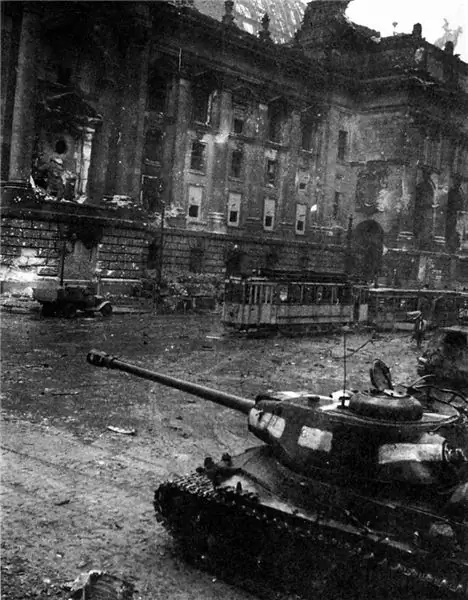
Ural SAG
Forskare i den sovjetiska tankindustrin, kandidat för historiska vetenskaper Zapariy Vasily Vladimirovich från Institute of History and Archaeology vid Ural Branch of the Russian Academy of Sciences i ett av hans verk beskriver i detalj de automatiska svetsningsenheter som används i Ural för pansar skrovsproduktion.
Det mest utbredda var ett attackgevär av typen "ACC" med ett Bushtedt -huvud. Det fanns åtta sådana installationer på Uralmash. Trådmatningshastigheten i denna maskin berodde på spänningen i bågen. Det krävdes 5 enheter, inklusive 3 kinematiska elmotorer och 1 motorgenerator.
Vid mitten av 1943 var svetsmaskinen SA-1000 konstruerad för IS-2: s tunga tankars behov. Eller en svetsmaskin med en kapacitet på upp till 1000 A.
För att bemästra tillverkningen av pansarskrov för den nya Chelyabinsk tunga tanken IS-3, konstruerade ingenjörerna i anläggningen 1944 apparaten "SG-2000". Denna maskin var konstruerad för att fungera med koldioxidsvetsade trådar med en ökad diameter (6-8 mm) och användes vid tillverkningen av IS-3-tornet. Installationen hade en dispenser för införande av en speciell komposition (olika järnlegeringar) i svetsdelen för att avoxidera (återställa) metallen i den. Totalt, på principen om självreglering av svetsbågen vid UZTM, 1945, skapades 9 autosvetsanläggningar av tre typer: "SA-1000", "SG-2000", "SAG" ("Automatisk svetsning huvud").
Vackrare än tysk rustning
Resultatet av hela historien med rustningen av tunga IS -stridsvagnar var en överraskande snabb utveckling av ett stålrecept som överträffade tysk rustning i sina taktiska egenskaper. TsNII-48 fick ett härdbart 120 mm stål, vars tjocklek vid behov kunde ökas till 200 mm.
Detta blev den viktigaste grunden för utvecklingen av efterkrigsfamiljen av tunga sovjetiska stridsvagnar.