Patriotism för den sovjetiska industrieliten kombinerades med ett gemensamt ansvar för slutresultatet
Interaktion mellan industrin hela tiden - både i det ryska imperiet och i Sovjetunionen, och idag - tillhörde inte den inhemska industrins styrkor. Till skillnad från Tyskland eller USA, där avtalsförpliktelser hade och har en oföränderlig och nästan helig kraft.
Ta till exempel förhållandet mellan ryska metallurger och maskinbyggare. Under andra halvan av 1800 -talet fick nya transporttekniska anläggningar och varv inte den erforderliga mängden industrimetaller från Ural gruvarbetare. Den senare ansåg det olönsamt att göra många relativt billiga valsade produkter, eftersom samma vinst gavs av en mycket mindre volym av dyrt takjärn. Den saknade metallen för bilaxlar, motoraxlar och skeppshud måste köpas utomlands. Först i slutet av seklet löstes problemet av de södra ryska metallurgiska anläggningarna, grundade av belgiska eller franska industrimän. I Uralen byggde fransmännen också en anläggning - Chusovskaya.
Det verkar som om sovjetiska tider inte var sådana infall. Dessutom gav de metallurgiska anläggningar som byggdes på 30 -talet landet metall som helhet. Men varje gång maskinbyggare begärde nya komplexa typer av valsade produkter, behärskade metallurgisterna dem i åratal eller till och med decennier.
Institutionell feodalism
Låt oss vända oss till Uralvagonzavods historia. Redan i sina första projekt var det planerat att använda massivvalsade stålhjul under de fyraxlade bilarna när konstruktionskapaciteten nådde sin designkapacitet, vars leverantör var planerad till den närliggande Novo-Tagil Metallurgical Plant. Den senare byggdes emellertid av metallurgiska avdelningen, och den skjuter upp konstruktionen av hjulvalsverket till 1938-1942, och inte i första hand. Som ett resultat började fallet inte före kriget. Och efter kriget var uthyrning av hjul inte alltför intresserade av metallurger. Resultat: fram till mitten av 50-talet lämnade Tagil-bilarna fabriken på kortlivade gjutjärnshjul istället för stål. Detta medförde stora förluster för järnvägsarbetarna, men det fanns inget val: antingen sådana bilar eller inga.
Samma sak hände med introduktionen av låglegerat stål i vagnbyggnaden. De lovade en märkbar minskning av rullvagnens egenvikt samtidigt som alla prestandaegenskaper bibehölls. Designerna på Uralvagonzavod började designa bilar av låglegerad metall i slutet av 30-talet, men deras serieproduktion började först under andra halvan av 50-talet, eftersom metallurgister varken tillhandahållit lämpliga valsade produkter eller järnlegeringar för gjutning av delar.
Det måste sägas att viruset av departemental feodalism påverkade maskinbyggarna själva. Sommaren 1937 utspelade sig en intressant historia som präglade den tidens förbindelser mellan myndigheterna. Huvuddirektoratet för metallurgiska företag skickade en order på fem tusen ton ämnen till Uralvagonzavod för den nyligen lanserade bandagefabriken i Novo-Tagil-anläggningen. Huvuddirektoratet för transportteknik var upprörd över intrånget i ett underordnat företag. Biträdande chef för huvuddirektoratet G. G. Den 11 juli skickade Aleksandrov ett brev till GUMP och Uralvagonzavod med följande uttalande:”Vi är oerhört förvånade över att lösningen på en så viktig fråga som att organisera produktionen av ett bandageämne i Uralvagonzavod genomfördes utan vårt deltagande, och ännu mer - vi fick inte ens en kopia av outfiten skickad till Uralvagonzavod … Jag ber dig att upprätta ett fast förfarande för att utfärda ämnen till våra fabriker endast efter överenskommelse med oss och genom Glavtransmash."
Som ett resultat nekades metallurgerna bandagestålet, påstås på grund av den tekniska omöjligheten att gjuta högkvalitativa göt i Uralvagonzavods butik med öppen spis. Under tiden, redan 1936, gjordes ett axiellt ämne här, och 1937 - göt för arkvalsning. Därför måste götarna för höljeskvarnen, som ligger några kilometer från UVZ, transporteras från Vyksa- och Kuznetsk -anläggningarna. Dessutom lämnade deras kvalitet mycket att önska, och leveransvolymerna var otillräckliga.
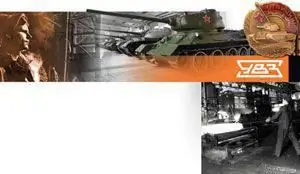
År 1938 upprepade sig historien. Huvudkonsumenten av UVZ -göt var Molotov (det vill säga Perm) Artillery Plant, som fick ett parti ämnen i slutet av året. Och bara ett fåtal av dem gick till bandagebutiken, som återigen fick importera den saknade metallen för två eller två och en halv tusen kilometer. Branschens intressen i distributionen av Uralvagonzavodsk stål var klart övervägande.
Avdelningssjukan skonade inte heller försvarsindustrin. Många publikationer om den sovjetiska tankbyggnadens historia är direkt fyllda med exempel på hur konstruktionen av prototyper eller utbyggnad av massproduktion försenades på grund av att metall inte levererades, särskilt rustning.
Och än idag har det sektoriella egenintresset inte gått någonstans, det har bara ändrat form. Begäran om nya formade rullade produkter bekämpas helt enkelt med orimliga priser. Det finns ingen anledning att tala om en samordnad politik. Efter rubelens växelkurs vid årsskiftet 2014-2015 höjde metallurgiska företag priserna på rullande materiel med 30-60 procent. Och de började genast klaga på maskinbyggarna för den utrustning som hade stigit i pris - trots allt produceras maskinerna i Ryssland och är inte bundna till dollarns växelkurs.
Det verkar som att i vårt land finns det bara ett botemedel för sektorsövergripande problem: skapandet av vertikalt integrerade system, där malmen som bryts av våra egna krafter först förvandlas till metall och sedan till färdiga maskiner.
Krigstidenhet
Det finns dock en kort period i vår historia när branschintressen har dragit sig tillbaka i bakgrunden. Vi pratar om det stora patriotiska kriget. Den sovjetiska industrielitens otvivelaktiga patriotism kombinerades med det gemensamma ansvaret för alla som deltar i försvarsproduktionen för slutresultatet. Det vill säga, chefen för den pansarvalsande anläggningen ansvarade inte så mycket för volymen smält och valsat stål, utan för antalet byggda tankar.
Huvudsteget i denna riktning gjordes av direktören för NII-48 A. S. Zavyalov. I de första dagarna av kriget vände han sig till regeringen med ett förslag om att instruera institutet att införa teknik för tillverkning av specialstål och pansarstrukturer på företag i östra landet, som först var involverade i tillverkning av pansar fordon. I början av juli ledde team av specialister från NII-48 den tekniska omstruktureringen av 14 största företag. Bland dem fanns Magnitogorsk och Kuznetsk metallurgiska växter, Novo-Tagil och Chusovka metallurgiska växter, Ural Heavy Machine Building Plant, Gorky Krasnoye Sormovo, Stalingrad Tractor Plant, Stalingrad Red October och nr 264. Således kränkte Zavyalov tabu före kriget: listan omfattade företag av tre personers kommissariater.
Patriotism och tvångsundertryckande av departementell egoism gav sovjetisk metallurgi oöverträffade utvecklingshastigheter för försvarsprodukter, varken under förkriget eller efterkrigstiden. På några månader organiserades produktionen av ferromangan, ferrosilikon, ferrokrom, ferrovanadium och andra legeringar i östra delen av landet (främst i Ural), utan vilken det är omöjligt att få rustningsstål. Efter förlusten av de västra regionerna förblev Chelyabinsk den enda ferrolegeringsanläggningen i Sovjetunionen. På den, på kort tid, ökades smältningen med två och en halv gånger. 25 typer av produkter producerades, men mest av alla var olika typer av ferrokrom. Smältning av ferromangan etablerades i masugnar, och inte bara i lågt tonnage gamla masugnar från Nizhniy Tagil- och Kushvinsky-anläggningarna, utan också i en stor modern ugn i Magnitogorsk Combine. I motsats till alla förkrigstidens tankar smältes ferrokrom under andra hälften av 1941 i sina masugnar av metallurger från Nizhniy Tagil- och Serov-anläggningarna, och forskare från Ural-avdelningen vid Sovjetunionens vetenskapsakademi gav stort stöd för att skapa ett nytt teknologi. Senare behärskades ferrosilisiumsmältning i masugnarna i Serov.
Det fanns inga pansarläger varken i Ural eller i västra Sibirien före kriget, de måste hastigt överföras från företag som befann sig i stridszonen.
Sommaren 1941 var den evakuerade utrustningen fortfarande under transport. Och sedan föreslog chefsmekanikern för Magnitogorsk Combine N. A. Ryzhenko att rulla rustningen på en blommande kvarn. Trots den stora risken genomfördes idén. Och i oktober trädde ett pansarläger, hämtat från Mariupol -anläggningen, i tjänst. Den monterades på bara 54 dagar. Enligt normerna före kriget tog detta ett år.
Novo-Tagil-anläggningen fick lägret från Leningrad. Förberedelserna för dess intagning började i juli, först antogs det att det skulle monteras på bandagets plats. Förbandslägret demonterades, men det visade sig att det gamla förrådet inte räckte till för att installera det pansarlägret och måste placeras någon annanstans. Kriget tvingades göra det som ansågs omöjligt förrän nyligen: för bara ett år sedan hade försök att utföra industribyggande med en integrerad "höghastighets" -metod i Nizhny Tagil i bästa fall delvis framgång, och sommaren 1941 mest komplex konstruktion var nästan perfekt. Den 10 september rullades den första Tagil -stålplåten en månad före schemat. Totalt erhölls i slutet av året 13 650 ton plåt, inklusive cirka 60 procent rustning (bruket testades på kolstål, och i oktober - december rullades kolstål med brist på rustningsgöt). Som ett resultat, redan i januari 1942, översteg den månatliga produktionen av pansarplattor vid Ural-fabrikerna sex månader i hela Sovjetunionen före kriget.
Inte mindre överraskande händelser ägde rum på andra lite kända företag. Under kriget var Zlatoust metallurgiska anläggning sämre än Magnitogorsk -skördetröskeln när det gäller volymen av smältning och valsat stål, men det överträffade det avsevärt i sin produktmix - cirka 300 legeringar och kolstål tillverkades här. Utan leveranser från Zlatoust skulle produktionen av många typer av vapen, främst tankmotorer, ha slutat.
Gamla Ural-fabriker visade sig vara oumbärliga vid tillverkning av små partier av särskilt högkvalitativt stål. Till exempel investerades metall från Serov Metallurgical, huvudtillverkaren av kalibrerade valsade produkter, i varje sovjetisk tank. Nizhnesalda -anläggningen bytte till nickeljärn och stålsmältning. Denna lista kan fortsätta i det oändliga - under krigsåren, där det fanns minst en kupol, smälts metall av vapen.
Det finns en nyfiken historia med flussmedel för automatisk svetsning. Före och i början av kriget smälts de till ett av Donbass -företagen, efter att ockupationen av vilka centraliserade leveranser helt upphörde. I slutet av 1941 började anställda vid Institutet för elektrisk svetsning vid Vetenskapsakademin i den ukrainska SSR leta efter substitutmaterial som finns tillgängligt i Ural i ett mer eller mindre användbart skick. Och de hittade dem - i form av masugnsslagg från Ashinskiy metallurgiska fabrik. Endast små förbättringar krävdes: masugnarna berikade sina slaggar med mangan och förvandlade dem därmed till ett helt lämpligt flussmedel. Utrustningen som var nödvändig för testning togs från Nizhny Tagil direkt till Asha.
Exempel på lokalt samarbete mellan tank- och metallurgiska anläggningar är mycket vägledande. Före lanseringen av sina egna anläggningar utfördes värmebehandling av tankdelar från Ural Tank Plant nr 183 vid Nizhniy Tagil Metallurgical Plant.
UTZ-gjuteriarbetarnas framgångsrika arbete underlättades avsevärt av hjälp från den närliggande eldstaden Nizhniy Tagil, som etablerade produktionen av högkvalitativa eldfasta flintproppar. Detta gjorde det möjligt att utföra problemfri gjutning av tunga rustningsstålsmältor för formgjutning.
1942-1945 drivs öppna spisar vid UTZ huvudsakligen på koksugn och masugnsgas från Novo-Tagil Metallurgical och Nizhniy Tagil Coke Plants. Gasledningen har varit i drift sedan februari 1942. Anläggning nr 183: s egen gasproducerande station gav inte mer än 40 procent av behoven.
Ibland var ett enkelt råd tillräckligt för att lösa ett problem. Informationen från lokala metallurger om en liten mangangruva som utvecklades på 1870 -talet hjälpte till att överleva flera veckor innan leveranserna av ferromanganer började utan att stoppa gjutningen av tankspår.
Ett annat exempel: när produktionen av pansarstål ökade kunde butiken med öppen spis inte längre hänga med i smältningen av metall för luftbombarnas huvuden. Det gick inte att få det utifrån. Direktör Yu. E. Maksarev erinrade om händelseförloppet i hans memoarer:”När jag var på ett av mötena i stadskommittén träffade jag direktören för den gamla, fortfarande Demidov -anläggningen och bad att få ta av mig gjutningen av bombhuvudena. Han sa: Jag kan inte hjälpa till med stål, men med råd kommer jag att hjälpa. Och när jag kom till hans anläggning visade han mig en och ett halvt ton Bessemer -omvandlare med medelblåsning. Han gav mig ritningarna och sa att han vet att vi har ett bra mekaniserat järngjuteri, och dina omvandlare kommer att svetsa”. Så här såg ordern för anläggningen den 8 september 1942 ut på organisationen i Griffin -hjulbutiken i Bessemer -sektionen med tre små omvandlare (ett och ett halvt ton metall vardera). Vid den 25 september förbereddes projektet av konstruktions- och teknikavdelningen för huvudbyggnadsledningen, specialisterna på chefsmekanikerns avdelning svetsade snabbt omvandlare och pannor - tankar för flytande järn. Testkörningen av Bessemer-avdelningen och gjutning av en experimentell sats med fem namn på delar ägde rum i början av oktober-november 1942. Serieproduktionen började i slutet av november.
I slutet av ämnet: samarbetet mellan metallurger och tankbyggare under krigstid agerade åt båda hållen. Installatörerna av Ural Tank Plant deltog i idrifttagandet av många nya enheter i Novo-Tagil Metallurgical Plant. I maj 1944 tillverkades ett betydande antal foderplattor för reparation av masugnen i den pansrade torngjutningsbutiken.
Men metallurgisternas huvudassistent var naturligtvis Ural Heavy Machine Building Plant. Orderböckerna för UZTM för 1942-1945 är bokstavligen packade med dokument om tillverkning av reservdelar och anordningar för metallurgiska ändamål - både för tankindustrins behov och för företagen i People's Commissariat of Ferrous Metallurgy. Hösten 1942 restaurerades officiellt en särskild division för tillverkning av utrustning för metallurgiska anläggningar vid UZTM. Den fick koden "Division 15" och var underordnad den biträdande direktören för upphandlingsbutiker och skrovproduktion.
Framgång i skärningspunkten mellan industrier
Samarbetet mellan metallurger och tankbyggare har lett till skapandet av ett antal tekniker som utan överdrift kan kallas verkliga vetenskapliga och tekniska genombrott.
Efter att ha smält och valsat pansarstål till plåtar överförde metallurger sina produkter till pansarskrovsproduktion. Här skars metallen enligt mallen i motsvarande delar. I produktionen av "trettiofyra" levererades särskilt mycket besvär av två delar av skrovet: stänkskärmar (den lutande sidan av sidan) och den vertikala sidoplattan. Båda var långa, även i breddband med sneda snitt längs kanterna.
Idén föreslog naturligtvis sig själv att rulla en mätlist lika bred på de färdiga delarna. Det formulerades först av pansarvagnarna på Mariupol -fabriken sommaren 1941. För provrullning valde vi ett slabbkvarn i Zaporizhstal, dit två sändningar av rustningsgöt skickades. Men då hann de inte komma igång: de framryckande tyska trupperna fångade både ekelonerna och Zaporozhye själv.
Vid årsskiftet 1941-1942, under evakueringen och utvecklingen av rustningstillverkning vid de nya fabrikerna, fanns det inte tillräckligt med rand. Men i maj 1942 fick People's Commissariat of Ferrous Metallurgy igen en order om att hyra den för T-34 och KV-tankar. Uppgiften visade sig vara svår: toleranserna i bredd bör inte överstiga -2/ + 5 millimeter, halvmåneformen (böjningen) för delens totala längd var 5 millimeter. Sprickor, solnedgångar och delaminering var inte tillåtna vid kanterna så att svetsning kunde utföras utan bearbetning eller flamskärning.
Experimentellt arbete började samtidigt i de rullande butikerna vid metallurgiska anläggningarna i Magnitogorsk och Kuznetsk, till en början utan några speciella prestationer. Uthyrningen av delar till KV-tankarna övergavs snart, men T-34 lyckades slutligen. Författarteamet som består av chefen för metallurgiska avdelningen vid NII-48 G. A. Vinogradov, chefsingenjören för KMK L. E. Vaisberg och ingenjören för samma anläggning S. E. står "900" för järnvägs- och konstruktionsbruket är en helt ny metod att rulla "på kanten". I januari 1943 utfärdades 280 remsor, i februari - 486, i mars - 1636 stycken. I april, efter alla nödvändiga tester, började utvecklingen av bruttoproduktionen av mätremsor för T-34-tankarnas hjulbågsfoder. Ursprungligen levererades de till UZTM och Ural Tank Plant, och sedan till andra fabriker - tillverkare av T -34 -tankar. Skrotet, som ursprungligen var 9,2 procent, hade sjunkit till 2,5 procent i oktober 1943, och de undermåliga remsorna användes för att göra mindre delar.
En fullständig och noggrann utvärdering av den nya tekniken ges av motsvarande rapport från TsNII-48 av den 25 december 1943: "En grundläggande ny metod för att rulla en bred pansarlist" på kanten "utvecklades, testades och infördes i bruttoproduktion, som fram till nyligen ansågs vara omöjligt i Sovjetunionen och utomlands. Att få en kalibrerad (uppmätt) remsa med en bredd på den färdiga delen av T-34-tankens pansarskrov gjorde det möjligt för NKTP-fabrikerna att anta en ny högpresterande teknik för tillverkning av pansardelar utan att skära längsgående kanter. Tack vare tillämpningen av den nya metoden på en av de huvudsakliga pansardelarna i T-34-tanken (stänkskärmar) uppnåddes en mycket betydande tidsbesparing (cirka 36%) när man klippte ut dem. Uppnått besparingar med 8C rustningstål upp till 15 procent och syrebesparingar på 15 000 cbm per 1000 skrov”.
I slutet av 1943 behärskades rullningen av en mätlist för en annan del av T -34 -skrovet - den vertikala delen av sidan. Det återstår bara att tillägga att författarna till denna uppfinning tilldelades Stalinpriset för 1943.
Samma år 1943, genom gemensamma ansträngningar från laboratoriet vid det ukrainska metallinstitutet (under ledning av PA Aleksandrov) och arbetare vid Kuznetsk Metallurgical Combine och Ural Tank Plant, utvecklades en särskild periodisk rullad profil och behärskades i produktionen för upphandlingen av massa och kritiska delar av de "trettiofyra" - balanseringsaxlarna. Den första experimentella satsen med en periodisk profil mottogs på KMK i december, i början av 1944 började serieproduktionen. I oktober bytte Ural Tank Plant helt till tillverkning av balanseringsaxlar från ett nytt ämne, i slutet av året gick UZTM med. Som ett resultat ökade produktiviteten hos smideshammarna med 63 procent och antalet delbrott minskade.
Tankbyggarnas framgångsrika arbete underlättades kraftigt av rullande materiel i bandagekvarnen i Novo-Tagil Metallurgical Plant. Från och med våren 1942 levererade de rullade axelremmar med reducerade bearbetningsbidrag, 1943 reducerades ersättningarna igen. I kombination med det nya skärverktyget gjorde detta det möjligt att utföra tidskrävande avskalning av axelremmar strikt enligt schemat och utan mycket stress. Ett sällsynt fall: Folkekommissären för tankindustrin V. A. Malyshev ansåg i sin order av den 28 september 1943 att det var nödvändigt att uttrycka särskild tacksamhet till Tagil -metallurgerna.
Och slutligen, det sista exemplet: 1943 började fälgarna på T-34-supporttankarna, först vid Chelyabinsk Kirov-fabriken och sedan på andra företag, tillverkas av speciella profilerade valsade produkter. Denna framgång noterades också i ordningen av V. A. Malyshev.
Det återstår att tillägga att specialisterna från det amerikanska företaget "Chrysler", efter att ha studerat T-34-85-tanken som fångades i Korea, särskilt noterade perfektionen hos de stålämnen som stridsfordonet tillverkades av. Och också det faktum att de ofta var fler än produkterna från de amerikanska metallurgiska företagen.